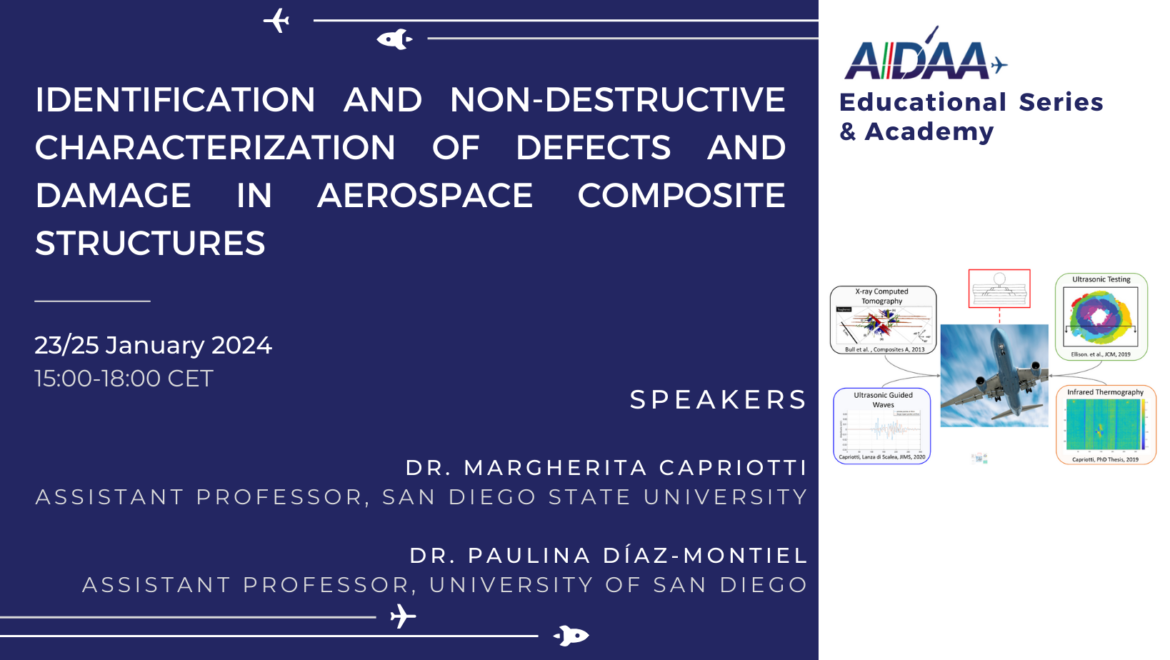
Identification and non-destructive characterization of defects and damage in aerospace composite structures
23/25 January 15-18 CET
Fiber-reinforced polymeric (FRP) composites are high-performance materials used in the aerospace industry due to their excellent fatigue resistance, durability, and high stiffness- and strength- to weight ratios. Composites allow the design of lightweight structures with tailorable properties that minimize energy usage and contaminant emissions. These materials are currently utilized in fuselages, wings, tails, doors, and interiors of modern aerospace structures.
Despite the excellent mechanical properties, adoption and certification of composite aerospace structures is a challenge primarily due to (1) the current knowledge gap in the technology, manufacturing, process-induced defects, maintenance and repair methods for aerospace-grade FRP composites, and (2) the complex and highly varying behavior and damage formation/evolution of these materials.
This course discusses some of the main challenges for the use of composite materials in aerospace applications, emphasizing four main aspects: manufacturing defects and signatures, identification of defects via non-destructive evaluation (NDE) methods, effect of defects on the mechanical performance, and NDE for assessment of structural integrity.
The current manufacturing techniques for fabricating aerospace-grade FRP composite structures are discussed. The common defects associated with these methods (e.g., fiber and ply waviness, voids/porosity, inclusions, resin-rich regions) are reviewed, and the effect of these manufacturing defects on the strength and life of composite structures is analyzed. The state-of-the art techniques for identifying and characterizing defects in aerospace structural components using NDE methods are discussed, giving particular attention to ultrasonic testing, guided waves, infrared thermography and X-Ray computed tomography. Finally, the current challenges for assessing structural integrity of aerospace composite structures via NDE techniques are presented and the main areas of opportunity in this field are highlighted.
MODULE 1 – Manufacturing Defects and Signatures (90 minutes)
- Overview of composite materials systems used in the aerospace industry.
- Manufacturing processes for aerospace composite materials.
- Defects developed during the manufacturing processes.
MODULE 2 – Non-destructive Evaluation Methods (90 minutes)
- Non-destructive evaluation (NDE) techniques for the detection and characterization of defects in the aerospace industry.
MODULE 3 – Effect of Defects (90 minutes)
- Experimental and modeling approaches for predicting the effect of defects on the damage modes and mechanical performance of composites.
MODULE 4 – Structural Integrity Assessment using NDE Methods (90 minutes)
- Damage developed in composites during operational life.
- NDE methods for assessment of structural integrity of composite structures.
Learning objectives
At the end of this course, the attendees should be able to:
- Explain the difference between thermoplastic and thermoset polymer systems, in terms of the microstructure and mechanical properties.
- List the main applications of carbon fiber reinforced polymeric (CFRP) composites in aerospace structural components.
- Explain the different manufacturing methods for fabricating aerospace-grade composite materials, and identify the advantages and disadvantages of each of these techniques.
- Describe the common defects in CFRP composites developed during the manufacturing.
- Describe the needs, constraints and outcomes of NDE inspections in the aerospace field.
- Understand the physical principles and basic implementation of the presented NDE techniques (i.e., ultrasonic testing, ultrasonic guided waves, infrared thermography, X-ray computed tomography).
- Assess the effect of manufacturing defects on the mechanical properties, strength and life of composite structures.
- Describe damage formation and/or evolution in CFRP due to fatigue, impacts and environmental conditions.
- Assess advantages and limitations of NDE techniques with respect to specific defects and damages in the aerospace field.
Target audience: undergraduate, graduate and doctoral students, academic and non-academic professionals. CTNA-Cluster Exploore Marche members.
Participation
You need to buy one of the package list available here and use the Order ID assigned to you after purchase.
You need to Login for registration.